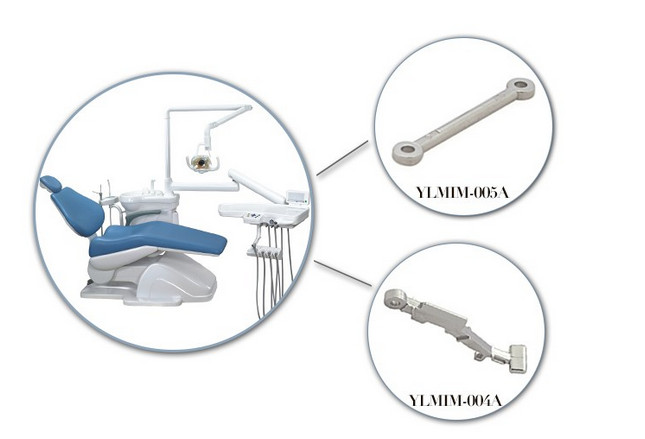
Application areas for MIM technology
Typical applications Aerospace industry: aircraft wing strands, rocket nozzles, missile tail fins, ceramic turbine blade cores; Automotive industry: components for ignition control locks, turbocharger rotors, valve guides, components for automotive brakes, components for automotive sunscreens; Electronics industry: disk drive components, cable connectors, electronic tube housings, computer print heads, electronic packages, heat sink materials; Military industry: mine rotors, gun plate triggers, armour-piercing bullet cores, collimators, small arrows for cluster projectiles; Medical devices: orthodontic brackets, internal sutures, biopsy forceps, radiation shields; Household products: watch cases, watch straps, watch clasps, golf heads and holders, sports shoe buckles, sporting gun parts, document binders and hole punchers; Machinery industry: shaped milling cutters, cutting tools, miniature gears;MIM advantages
1, high degree of freedom of part geometry, one time forming production of complex-shaped metal parts; 2, MIM products have uniform density, good finish, surface roughness can reach Ra 0.80 ~ 1.6μm, weight range of 0.1 ~ 200g. high dimensional accuracy (±0.1% ~ ±0.3%), generally without subsequent processing; 3, wide range of applicable materials, wide application areas, high utilization rate of raw materials, high degree of production automation, simple procedures, continuous mass production can be achieved; 4, stable product quality, reliable performance, the relative density of products can reach 95% to 99%, can be carburized, quenched, tempered and other heat treatment. The products have high mechanical properties such as strength, hardness and elongation, good wear resistance, fatigue resistance and uniform organization;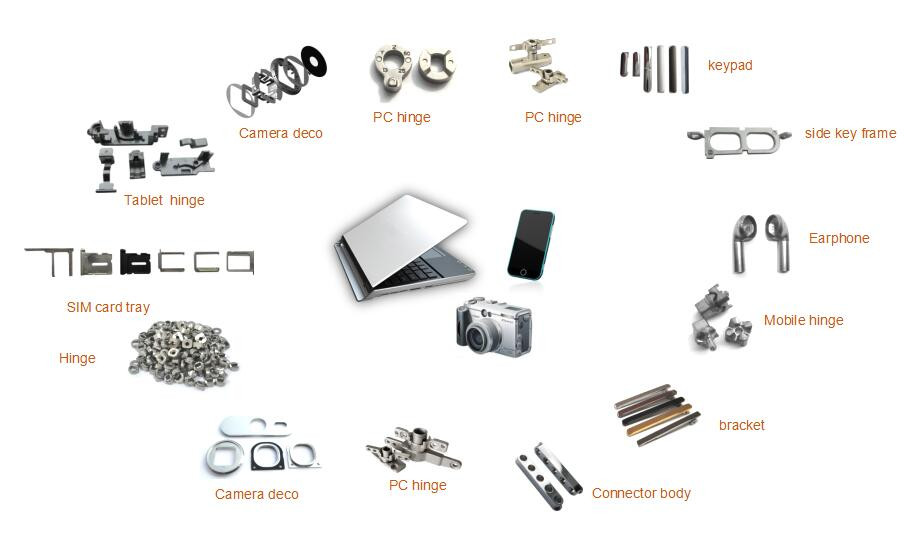
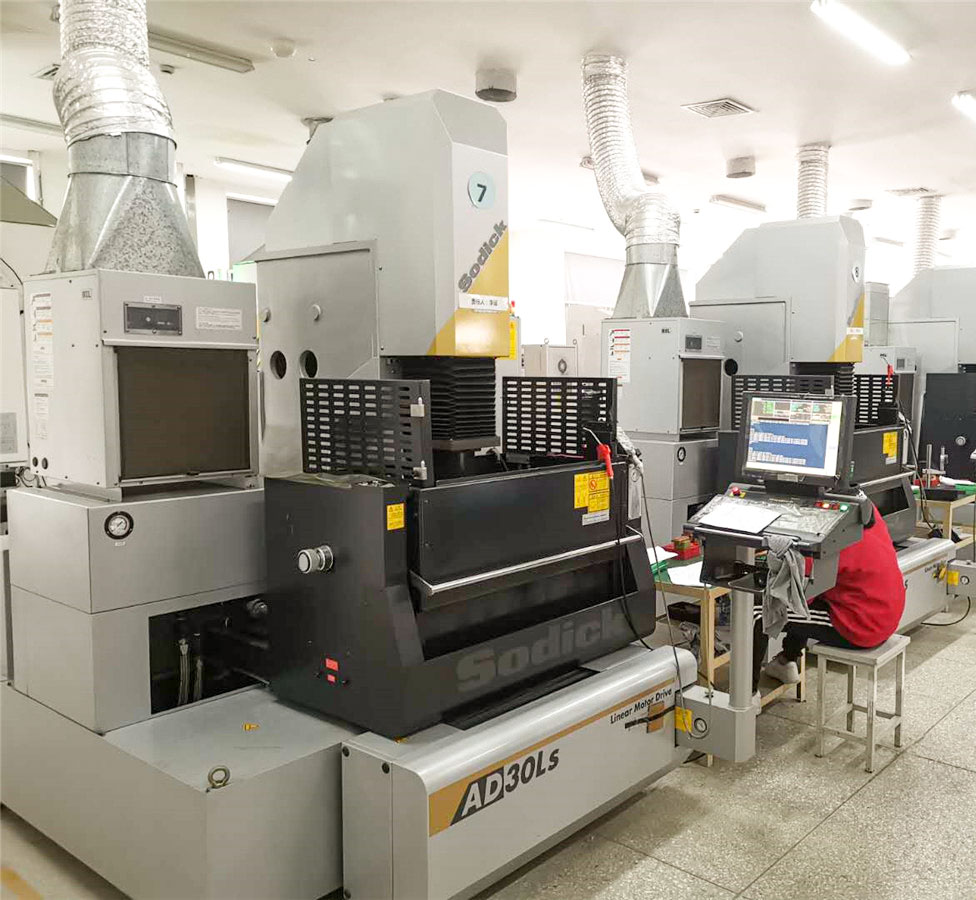
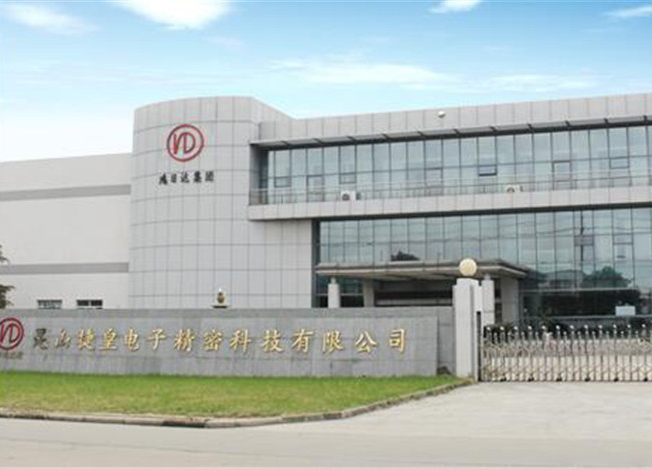
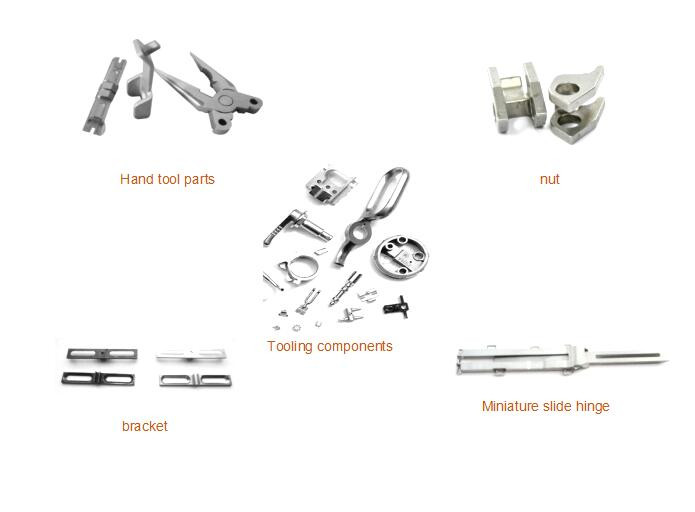
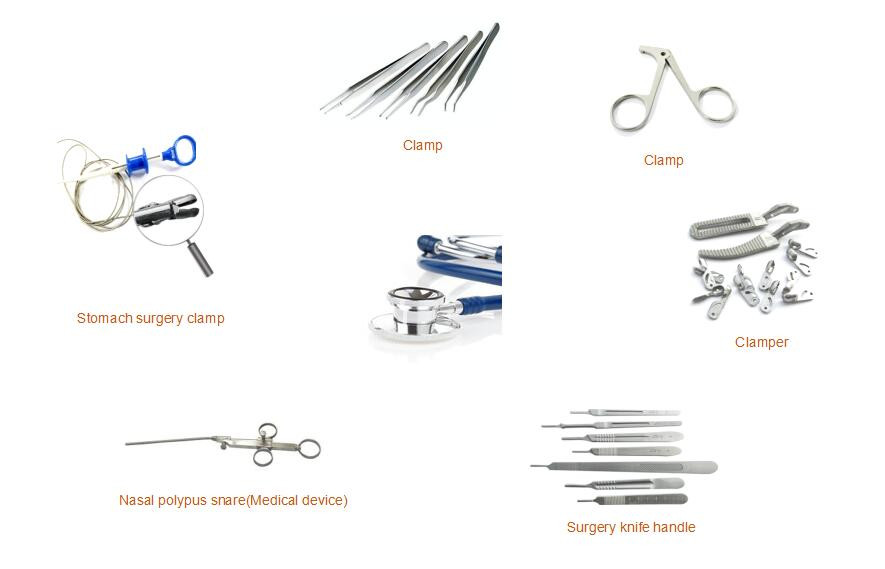
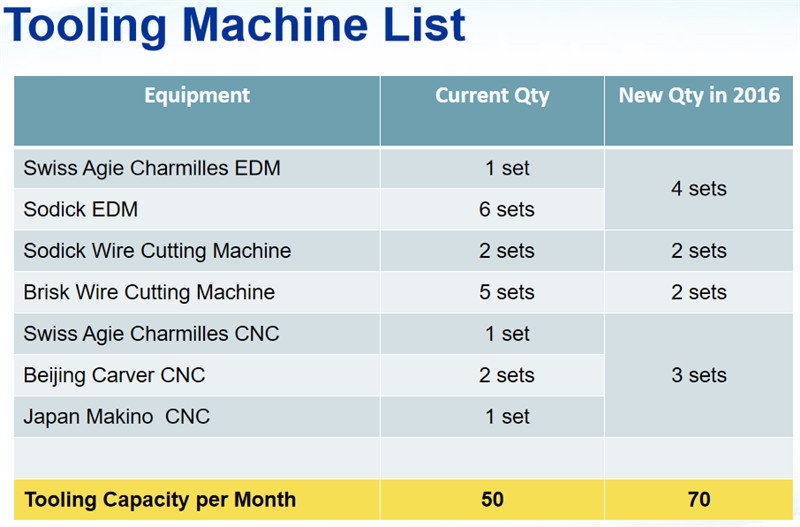

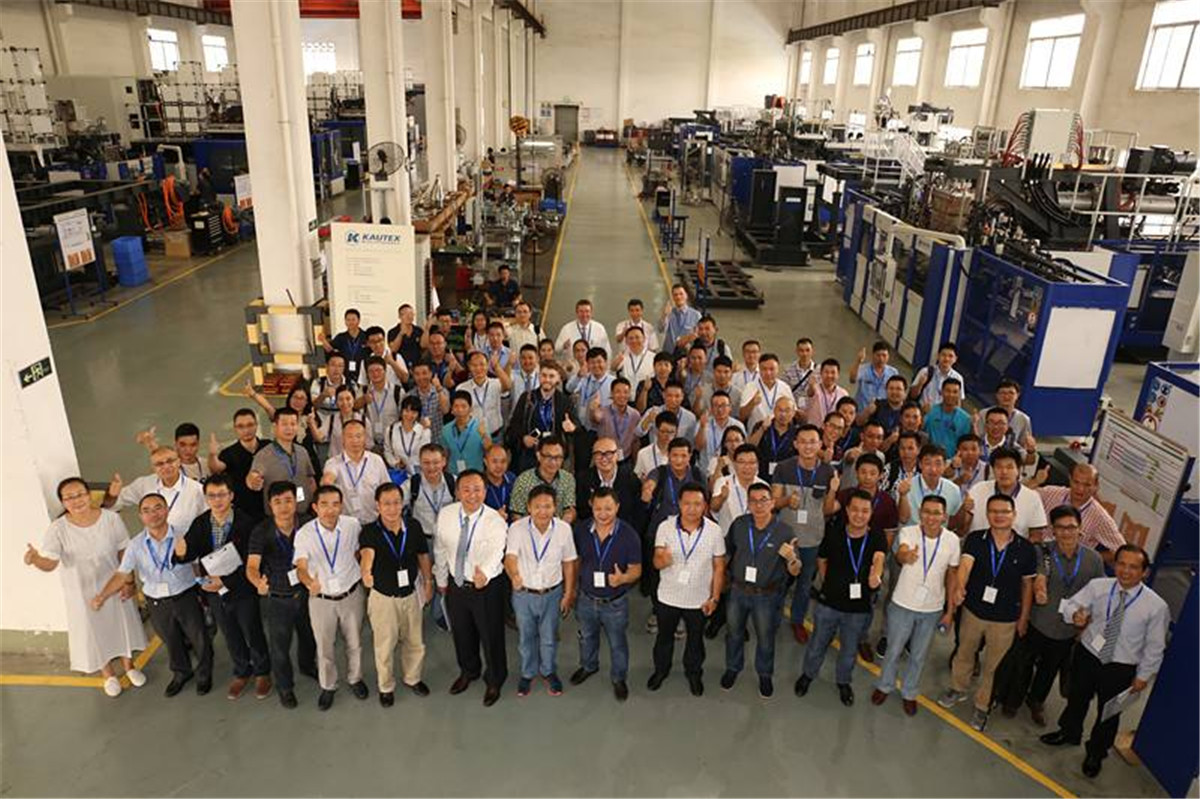
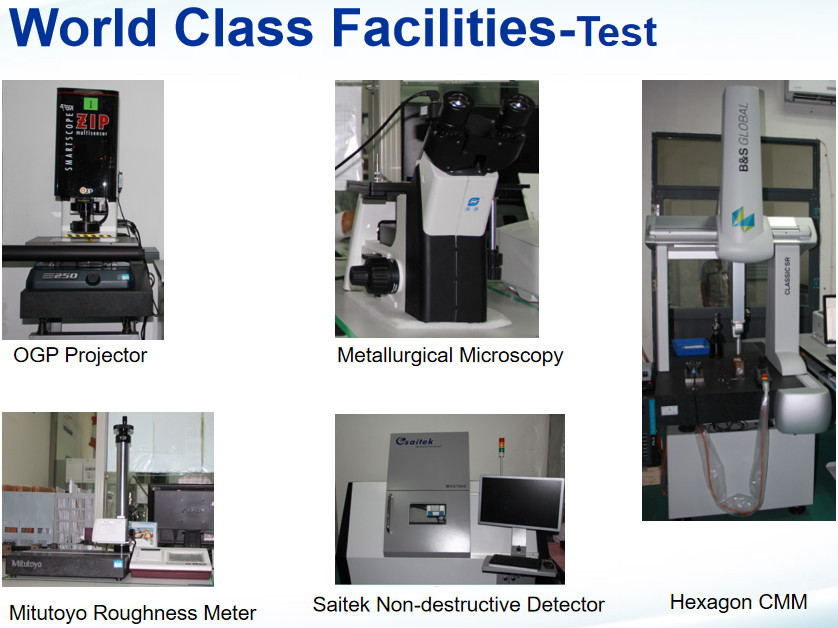
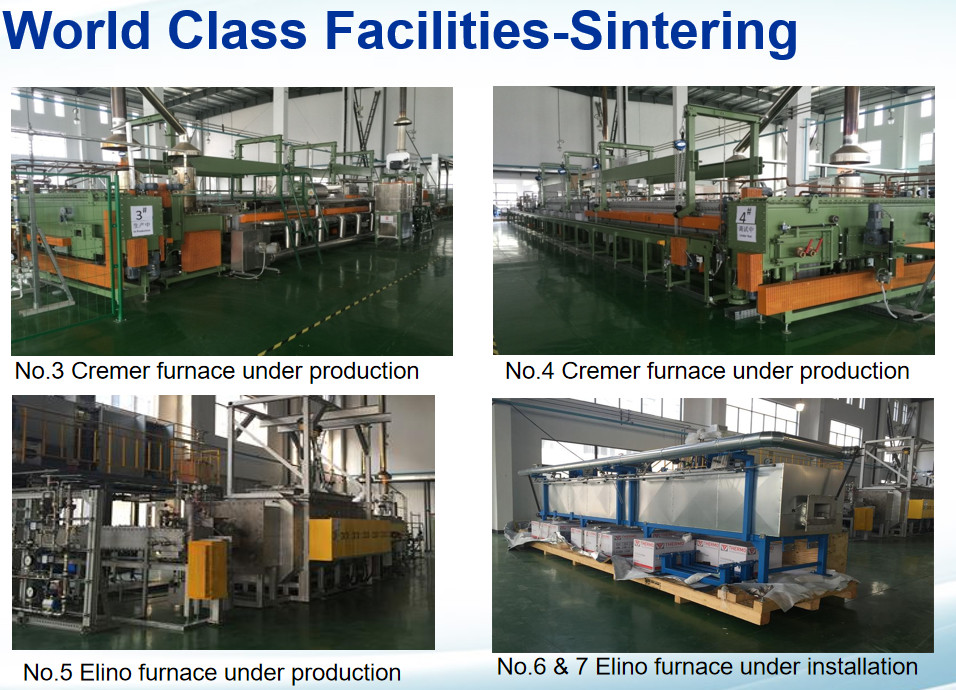
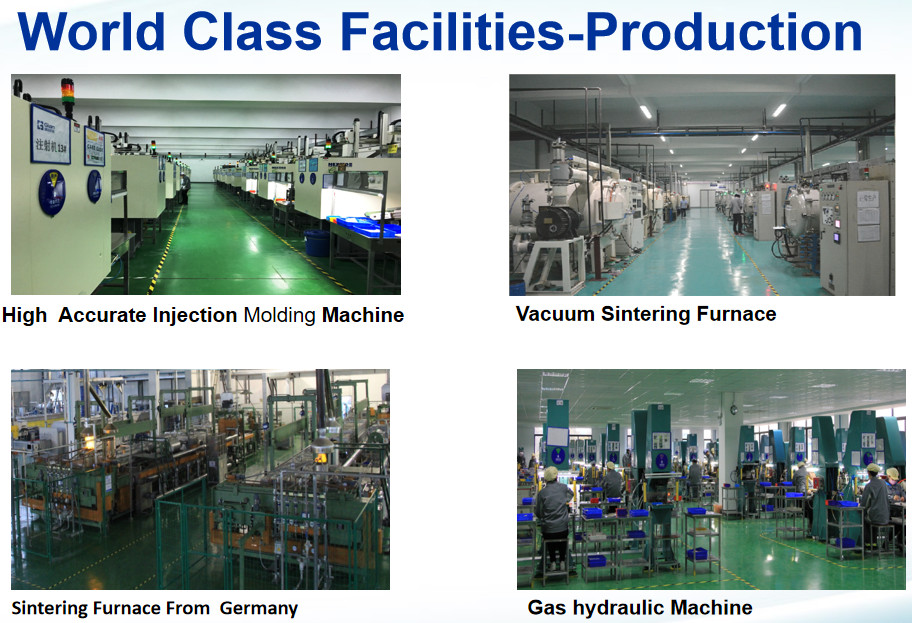
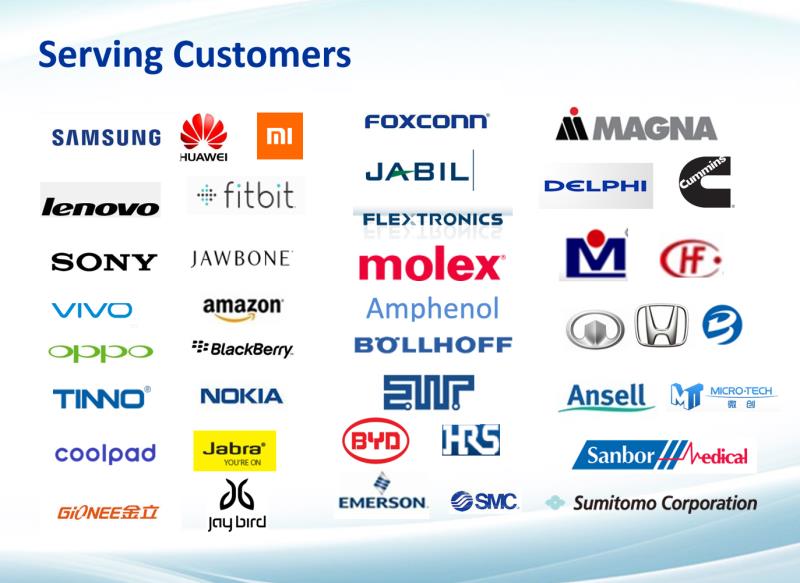